A primary reason for the scarcity of PFS capacity is that many manufacturing facilities were originally designed for vial filling, with PFS capabilities added later as an afterthought. This retrofit approach results in limited PFS capacity, further complicating the production landscape. Additionally, the complex formulation and handling requirements of products designed for PFS demand significant expertise and training, which many small companies cannot afford. Long lead times and the high cost of PFS further exacerbate the issue, leaving small companies struggling to secure the necessary resources.
The demand for PFS capacity is high, with larger pharmaceutical companies often having priority access to manufacturing facilities. This leaves smaller companies in a challenging position, struggling to secure slots in an already crowded marketplace. The limited availability of contract manufacturing organizations (CMOs) specializing in PFS adds to the difficulty, as these organizations are often booked well in advance.
Technology Transfer and Supply Chain Complexities
Scaling from small-scale clinical trial production to large-scale commercial production involves complex technology transfer processes. Managing the supply chain for components, such as syringes, needles, and caps, is another hurdle, particularly when scaling up production. Small companies may lack in-house expertise in PFS manufacturing, necessitating reliance on external partners.
Limited Budgets
Small companies with limited milestone-driven funding should balance the higher costs of prefilled syringes against their benefits, such as improved patient adherence and outcomes. They can achieve this through early planning and budgeting, phased implementation with pilot programs, exploring diverse financing options, partnering with flexible CDMOs, leveraging patient feedback, optimizing costs, and streamlining regulatory approvals. By focusing on patient-centric strategies and continuous process optimization, these companies can effectively manage resources and justify their investment in PFS despite financial constraints.
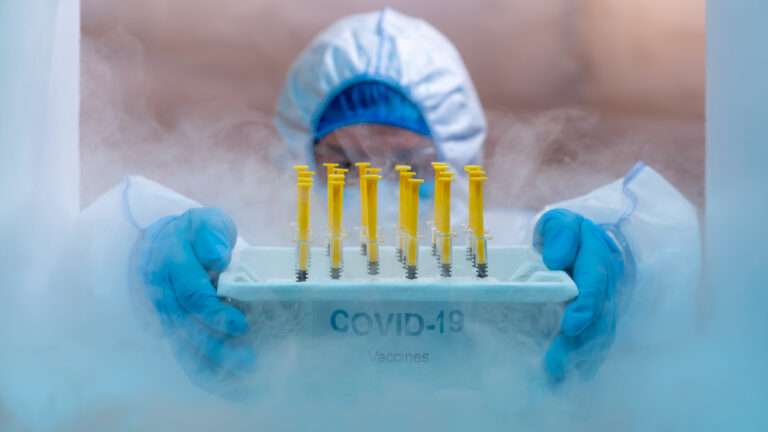
An effective strategy for small companies is to profit-share with their product manufacturers. This enhances collaboration and creates capacity for small companies to scale up production.
Determining if PFS is the Right Fill-Finish Option
Small companies must also decide whether or not PFS is the right option for their formulation. When deciding on the right fill-finish option, many factors must be considered:
1. Drug Characteristics
The unique properties of each drug dictate the requirements for the fill-finish process. Key characteristics to evaluate include:
- Viscosity: High-viscosity drugs may need specialized equipment and techniques for accurate dosing and smooth filling.
- Stability: Drugs with stability issues might require specific storage and handling conditions during the fill-finish process.
- Potency: High-potency drugs necessitate stringent containment measures to ensure safety and prevent cross-contamination.
- Release Profile: Extended-release formulations may need precise control over the fill-finish process to maintain their release characteristics.
2. Fill-Finish Options
Various fill-finish options should be carefully evaluated to determine the best fit for your drug:
- Aseptic vs. Terminal Sterilization: Aseptic fill-finish is often required for sensitive biologics, while terminal sterilization might be better suited for more stable small molecules.
- Prefilled Syringes vs. Vials: Prefilled syringes offer convenience and dosage accuracy but can be challenging for viscous formulations. Vials are more versatile but less convenient for end-users.
- Customized Solutions: Customizable equipment and processes can be tailored to handle unique drug properties effectively.
3. Technology and Equipment
The choice of technology and equipment plays a crucial role in the fill-finish process:
- High-Viscosity Handling: Specialized pumps and filling systems designed to handle high-viscosity formulations are necessary.
- Containment Systems: High-potency drugs require isolators or closed systems to protect operators and prevent contamination.
- Precise Dosing: Advanced dosing technologies can ensure accurate filling, which is crucial for extended-release formulations to maintain their therapeutic profile.
4. Regulatory Compliance
Regulatory compliance is vital throughout the fill-finish process:
- GMP Standards: Ensuring that the fill-finish process complies with Good Manufacturing Practices (GMP) is important for regulatory approval.
- Documentation and Validation: Comprehensive documentation and validation of the fill-finish process are necessary to demonstrate compliance and ensure quality.
5. Process Optimization
Continuous process optimization is crucial for addressing challenges and improving efficiency:
- Formulation Adjustments: Minor adjustments to the drug formulation can improve its compatibility with the fill-finish process.
- Process Development: Developing and optimizing the fill-finish process through small-scale trials and iterative testing can help address specific challenges.
- Experience: Leveraging prior experience with similar products and a proven history of manufacturing parenteral products in PFS can improve your chances of success.
6. In-house versus External Manufacturing
Evaluating cost-effective solutions for prefilled syringes involves comparing in-house versus external manufacturing:
- In-house Manufacturing: This option offers better control but requires substantial upfront costs and specialized expertise.
- External Manufacturing: Provides flexibility and access to specialized skills at potentially lower initial costs. Consideration should be given to revalidation costs, regulatory approvals, and potential delays if switching drug delivery formats in later stages.
How an Experienced Partner Can Help
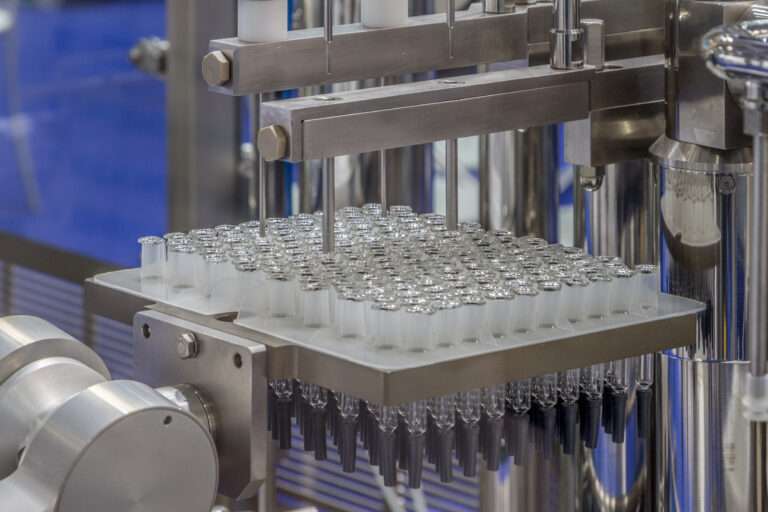
Pharmaceutical International Inc. (PII) is an ideal partner for prefilled syringes due to our extensive expertise and capabilities in handling complex formulations and scalable manufacturing. We offer flexible, cost-effective solutions, making us suitable for small companies with milestone-driven funding. Our automated technology and experienced team can manage high-viscosity, extended-release, and high-potency drugs, ensuring quality and compliance with regulatory standards.
PII supports both pilot programs and large-scale production, with streamlined processes for potential format changes, helping to mitigate risks and optimize costs. We work with small companies from start to finish, assisting them through clinical trials, process validations, and commercialization. Our diverse, experienced workforce can handle difficult-to-manufacture products, ensuring our clients' needs are met.
Conclusion
Navigating the complex landscape of PFS manufacturing can be daunting for small pharma companies, but by working with an experienced, knowledgeable partner, like PII, and developing a strategic approach, it is possible to achieve success and bring innovative therapies to market.
ABOUT Pii
Pharmaceutics International, Inc. (Pii), A Jabil Company, is a US-based contract development and manufacturing organization (CDMO) located in Hunt Valley, Maryland. The experienced scientists, engineers, and staff at Pii pride themselves on adroitly employing a phase appropriate method of drug development for the prudent use of their customer’s resources as they solve challenging problems. In addition to offering end-to-end development services, Pii manufactures a variety of dosage forms to include complex parenteral drugs and has a wealth of analytical testing capabilities. Its Hunt Valley campus has four aseptic suites with lyophilization capabilities. Our talented professionals stand ready to help!